<span> </span>
- Skip advertAdvertisement - Gallery continues below
<span>Radius arms - All bolt heads, nuts and threads are wire brushed and soaked with easing fluid. These two hold the rear radius arm to the rear axle.</span>
- Skip advertAdvertisement - Gallery continues below
<span>The rear radius arm’s chassis attachment bolt is treated similarly. This work is done first to allow the fluid to penetrate all threads.</span>
<span>Each of the radius arm to axle bolts are released using a 22 mm AF spanner on the bolt, and a 24 mm on the nut.</span>
- Skip advertAdvertisement - Gallery continues below
<span>The rearmost bolt is drifted out using a small diameter steel punch (small enough to avoid distorting the end of the bolt and its thread).</span>
<span>The forward bolt attaching the radius arm to the axle won’t slide out because it contacts the anti-roll bar link bracket on the axle casing.</span>
- Skip advertAdvertisement - Gallery continues below
<span>So Andy removes the bolt (22 & 24 mm AF again) holding the forward end of the radius arm to allow the arm to twist.</span>
<span>The radius arm can now be tilted inward slightly to allow that rear bolt to be extracted. The arm is then removed to the bench.</span>
- Skip advertAdvertisement - Gallery continues below
<span>To see exactly what is being dealt with, the joints between the old bushes and the radius arms are wire brushed clean.</span>
<span>The axle end bushes are easily pushed out on the press, their nylon outer sleeves sliding easily through the bore of the radius arm.</span>
- Skip advertAdvertisement - Gallery continues below
<span>The bush in the chassis end of the arm is bonded to an external steel sleeve which is an interference fit in the arm.</span>
<span>The steel sleeve of the chassis end bush is difficult to press out. The press pushes out just the rubber part, leaving the sleeve behind.</span>
- Skip advertAdvertisement - Gallery continues below
<span>This hollow (51 mm O/D x 8 mm thick) mandrel has sheared the rubber from its outer sleeve as the press pushed it down.</span>
<span>The steel sleeve is removed by first cutting along its inner length with a hacksaw, keeping the blade level, and avoiding cutting into the arm.</span>
- Skip advertAdvertisement - Gallery continues below
<span>The hammer and chisel is used to distort and finally cut the sleeve, until it folds inwards sufficiently to be driven out.</span>
<span>With the old bush sleeve removed. The arm’s bore is cleaned, any tool marks removed, then lubricated to help the new bush slide in.</span>
- Skip advertAdvertisement - Gallery continues below
<span>The new Polybush is positioned on the radius arm, and a spacer (drilled to clear the bush’s inner steel tube) is placed over the bush.</span>
<span>The hydraulic press gently forces the bush into the arm, with alignment being checked all the way down, until the spacer contacts the arm.</span>
- Skip advertAdvertisement - Gallery continues below
<span>The bush still needs to be further in, so the spacer is replaced by a socket of the correct O/D to push on the bush’s outer sleeve.</span>
<span>Each of the twin bushes at the axle end comprises a three piece set: the orange bush in two halves, and the centre steel tube.</span>
- Skip advertAdvertisement - Gallery continues below
<span>The new axle end bushes can be easily pressed in by hand, after first cleaning and lubricating the bores in the radius arm.</span>
<span>With the arm turned over, the other halves of the bushes are pushed into place, and the central steel tube is pushed through.</span>
- Skip advertAdvertisement - Gallery continues below
<span>Before refitting the arm, all bolts are treated with anti-seize grease, and this forward axle end bolt (see caption 5) is set in position.</span>
<span>Here, Kevin lifts the re-bushed radius arm into position and fits the restricted forward axle bolt first to secure the arm.</span>
- Skip advertAdvertisement - Gallery continues below
<span>With that bolt pushed through, the radius arm can now be pivoted to align the rearmost axle bolt and the forward chassis bolt holes.</span>
<span>Finally, Andy fully tightens the bolts, torquing them to 230 Nm for this vehicle (check the torque value for other vehicle types).</span>
- Skip advertAdvertisement - Gallery continues below
<span>Watts linkage to chassis: The bolt at the chassis end of the left hand link is removed (21 mm AF bolt head, 22 mm nut). Axle pivot linkage seen at right.</span>
<span>The inboard bolt at the differential mounting is withdrawn (19 mm bolt head, 21 mm nut) and the link removed onto the bench.</span>
- Skip advertAdvertisement - Gallery continues below
<span>As with the radius arm to axle bushes, this Watts link bush also has a nylon outer sleeve, so it should come out easily.</span>
<span>Again, the arm is supported accurately, and a correctly sized mandrel or socket is used with the press to push the bush out.</span>
- Skip advertAdvertisement - Gallery continues below
<span>With the old bushes removed from each link, it’s obvious that they are past their best, with one nylon outer sleeve breaking up.</span>
<span>The bore in the arm is cleaned with emery cloth and lubricated ready to accept the new Polybush and its steel centre tube.</span>
- Skip advertAdvertisement - Gallery continues below
<span>This Polybush also has a tapered leading edge (right of picture) which must be entered into the bore first to make fitting easier.</span>
<span>These Watts linkage bushes can be fitted using the hydraulic press as pictured, or simply squeezed in using a vice.</span>
- Skip advertAdvertisement - Gallery continues below
<span>With the bush fully in, the link is turned over to check the lip of that leading edge has expanded over the face of the arm.</span>
<span>The central steel tube can now be pushed into the new bush, squeezing with a vice and protective wood packing if needed.</span>
- Skip advertAdvertisement - Gallery continues below
<span>The link is now refitted with greased bolts, and tightened to a torque of 140 Nm (chassis) and 155 Nm (axle end) for this vehicle.</span>
<span>Panhard rod: Here is the Panhard rod (arrowed) bolted between the chassis bracket (left of pic), and the bracket on the axle (right).</span>
- Skip advertAdvertisement - Gallery continues below
<span>The Panhard is held at each end by a bolt and nut (24 mm AF). The nuts may be tight, and the bolts may need levering out.</span>
<span>Removal of the old bushes is a similar procedure as seen above, here pressing the bush out into a hollow tube underneath.</span>
- Skip advertAdvertisement - Gallery continues below
<span>In this case, the steel centre tube is fitted before pressing the new bush into the housing – the procedure works either way.</span>
<span>The tapered leading edge is entered first as the bush is pressed in, and then checked to confirm it has spread out over the housing.</span>
- Skip advertAdvertisement - Gallery continues below
<span>The Panhard rod is refitted to the vehicle with bolts well greased, and torqued to 230 Nm. That’s it, the D2 is rebushed.</span>
Recommended
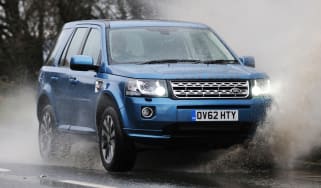
Land Rover Freelander on track for a comeback, but the UK will have to wait
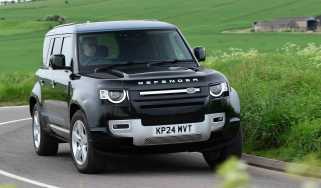
Land Rover Defender drives JLR profits to a ten year high
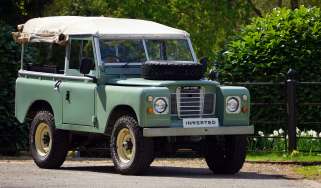
Classic Land Rovers get all-electric power thanks to Inverted
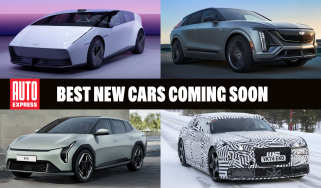
Best new cars coming soon: all the big new car launches due in 2025, 2026 and beyond
Most Popular
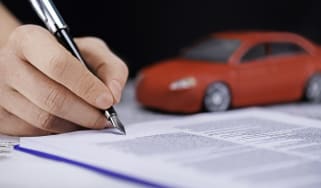
Avoid using car finance claim firms, says financial watchdog
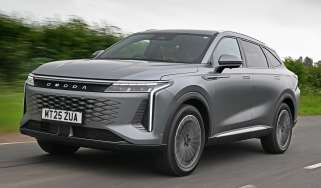
Omoda 9 review
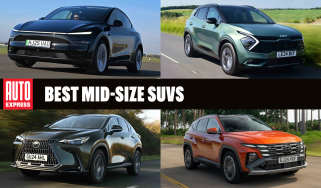
Best mid-size SUVs to buy 2025 - our expert pick of the top options