Upgrade the cab heater blower on your series III - pictures
Recommended
Land Rover Defender review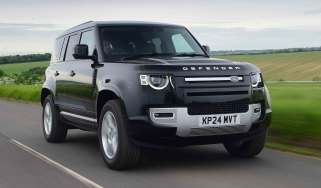
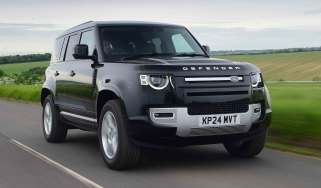
Land Rover Defender review
The Defender remains one of the most desirable SUVs around, offering a combination of genuine off-road ability, style and practicality
New Land Rover Defender Trophy Edition 2025 review: a family SUV for every terrain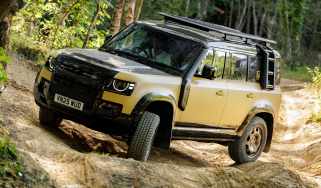
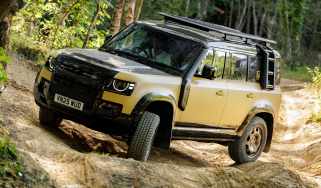
New Land Rover Defender Trophy Edition 2025 review: a family SUV for every terrain
The new Trophy Edition is a practical way to enjoy your next expedition
New Land Rover Defender Octa Black will be hard to spot in the dark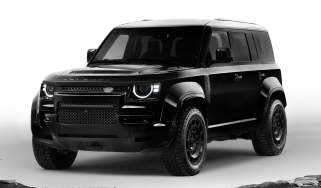
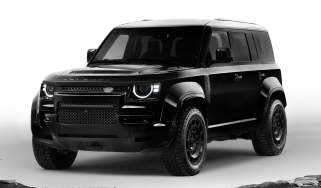
New Land Rover Defender Octa Black will be hard to spot in the dark
The “all-black interpretation” of Defender flagship has no fewer than 30 exterior elements finished in gloss or satin black
New Land Rover Defender Trophy Edition will make you feel at home in the Sahara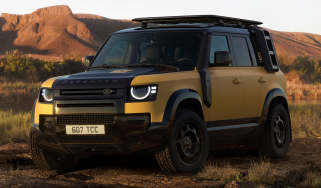
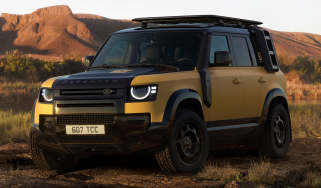
New Land Rover Defender Trophy Edition will make you feel at home in the Sahara
The Land Rover Defender Trophy Edition will likely find a home in the football ground carpark, but it could do the desert too…